Are you feeling torn between using a material takeoff and bill of quantities for your next construction project? You’re not alone! Figuring out which method is right for the job can be tricky, especially if you don’t know what each approach entails.
Luckily, you’ve come to the right place. In this blog post, we’ll cover the differences between MTOs and BOQs so that you can confidently make an informed decision about which is best suited to your needs. Read on to learn more!
What is Material Take Off
Material takeoff is an essential part of any construction project. It’s simply the process of determining and listing all the materials required to complete a job. It can include anything from lumber and drywall to nails and screws—whatever is necessary to get the job done!
It will help ensure that no material is overlooked or forgotten, which can save time and money in the long run. With material takeoffs, the project will run smoother and have better success overall.
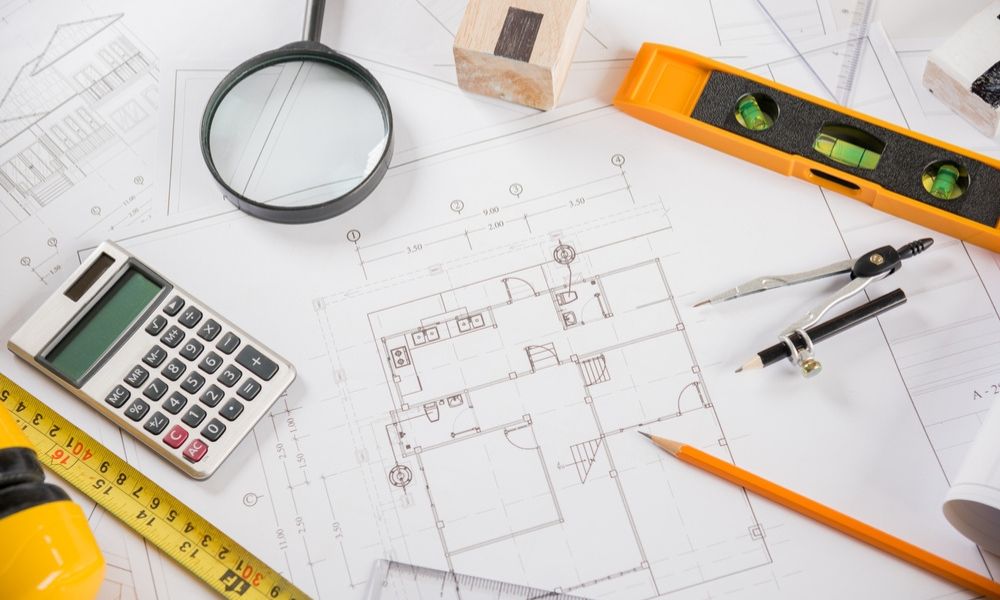
Benefits of Material Take Off
It is a process of calculating the material needs for a construction project. Given the complexity of material requirements, many businesses use material takeoff to quickly obtain accurate information and ensure that sufficient materials are ordered in advance.
The benefits of material takeoff include time savings when it comes to material calculations on projects and improved order accuracy due to better data-driven decisions.
With an MTO, it’s easier to keep track of material costs throughout the lifecycle of the project, including pre-construction estimates, progress payments, and overall budget compliance. Thus, It can provide results to avoid unnecessary costs or delays when planning for a successful construction project.
Disadvantages of Material Take Off
Making material take-offs can sometimes seem like a necessary evil, especially in large construction projects. Although It provides essential information about the material and labor needed for each stage of a project, it does come with some drawbacks.
Aside from being a time-consuming, tedious process, It can also lead to inaccurate results if all the factors of the build aren’t taken into account.
Additionally, It is highly prone to human error, which can result in costly material contingencies or delays. However, these risks can be managed by leveraging technology that automates the material takeoff process while ensuring accuracy and precision.
What is Bill of Quantities
It is a document used primarily in construction and engineering projects that breaks down the list of works into individual components. This bill lists the materials, labor, and plant required and associated costs for each component.
It’s an essential tool for providing accurate measurements and cost estimates for construction projects, helping to ensure that projects stay on schedule and within budget. For anyone working in construction, it should be important to understand the bill of quantities as it helps them plan ahead.
Benefits of Bill of Quantities
The bill of quantities is an extremely useful tool for any construction project. It allows for accurate and detailed cost estimates, enabling faster decision-making on projects in terms of resource planning and scheduling. This bill provides the exact breakdown of materials and labour, so everyone involved in the project can be reassured that each and every aspect is planned out with precision.
With a bill of quantities to refer to, it enables teams to accurately budget their finances and prioritize what resources are needed first or allocated as necessary. Using a bill of quantities also makes administration easier and more efficient as there is complete transparency at every stage of the project. In short, this bill streamlines the entire process and helps everyone involved reach success!
Disadvantages of Bill of Quantities
One of the biggest disadvantages is how the bill of quantities doesn’t allow for much flexibility since it fixes everything at one point. This may lead to bill increases when changes arise due to unexpected events.
It can also increase the bureaucratic burden on contractors or building owners, as they will have numerous documents related to the bill of quantities process that adds even more labor costs if changes need to be made. Billing for any additions or edits must be very detailed and completed in order for payment cycles to complete in a timely manner.
Another drawback to the bill of quantities is that it can take longer than other billing methods since it requires price estimates before submitting bids, which may take time depending on the complexity of the project. All in all, It might not always be the most efficient option in certain circumstances, despite its clear breakdown of components and services involved in a project.
Conclusion:
There are a few key things to remember when trying to decide whether to use a material takeoff or a bill of quantities for your next project. If you need more control over the budget and want to avoid cost overruns, then opt for the bill of quantities.
On the other hand, if you’re working with an experienced contractor who can provide accurate estimates, then go with the material takeoff. No matter which route you choose, make sure you understand all the pros and cons before making a decision.
Ready to Save on Your Next Construction Project?
Understanding the difference between a Material Take-Off and a Bill of Quantities can make a big impact on your budget. Whether you need detailed material estimates or a comprehensive cost breakdown, choosing the right method can help you avoid overspending.
Get Accurate Estimates and Reduce Costs Today!
Our expert team is ready to assist with precise material take-offs and comprehensive bills of quantities tailored to your project. Don’t leave your savings to chance—reach out to us for a consultation now.
Contact us to start maximizing your savings and optimizing your project’s success!