In any construction project, precise planning and accurate estimates are essential for success. One critical component of this process is the Material Take-Off (MTO). Understanding what an MTO is, why it’s important, and how to perform it efficiently can make a huge difference in project timelines, costs, and overall execution.
In this guide, we will walk through everything you need to know about Material Take-Offs, providing you with practical insights, tips, and the tools you need to streamline your construction projects and maximize efficiency.
What is a Material Take-Off?
A Material Take-Off (MTO) is the process of determining the quantities of all materials required to complete a construction project. It involves extracting material quantities from construction plans, drawings, and specifications. This list of materials serves as the foundation for creating cost estimates, procurement plans, and project schedules.
The MTO is performed by estimators, project managers, or quantity surveyors, and it covers materials such as concrete, timber, steel, plumbing supplies, and electrical wiring. The accuracy of the take-off process is critical for ensuring that the right amount of materials is ordered and that costs are controlled.
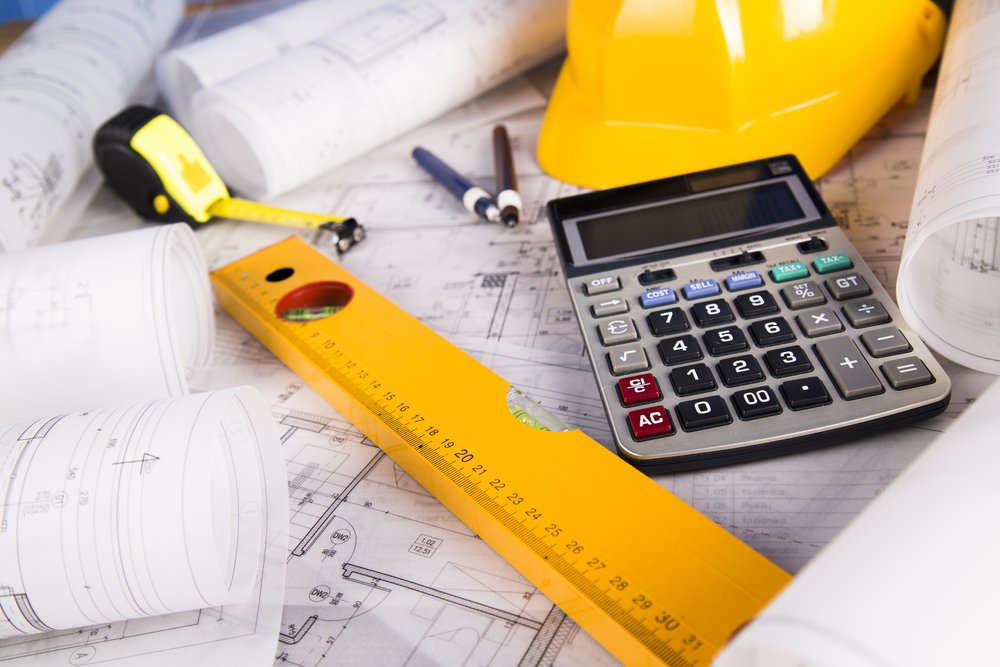
Why is a Material Take-Off Important?
Performing an accurate Material Take-Off is essential for several reasons:
1. Cost Control
The MTO process ensures that you have a clear understanding of the materials needed to complete the project. By calculating the exact quantities, you can avoid overordering, which leads to unnecessary costs, and underordering, which can cause delays and increased expenses. The MTO is the foundation of your project’s budget and cost estimate.
2. Efficient Procurement
An accurate MTO enables efficient procurement planning. By knowing exactly what materials are required, when, and in what quantities, you can coordinate deliveries to ensure that materials arrive on-site when needed, avoiding both storage issues and project delays.
3. Minimizing Waste
Overordering materials can lead to excess stock that may never be used, while underordering may require rushed orders or emergency deliveries, which often come at a premium price. By ensuring precise material calculations, an MTO reduces the risk of waste and optimizes the use of resources.
4. Improved Project Planning
Accurate material estimates are vital for developing realistic project schedules and ensuring smooth execution. By identifying material requirements early, project managers can better plan workflows, schedule labor, and anticipate any potential supply chain issues.
How is a Material Take-Off Performed?
Performing a Material Take-Off involves several key steps. Let’s walk through the process in detail.
1. Review Project Drawings
The first step in any Material Take-Off is to thoroughly review the project’s construction drawings and blueprints. These include architectural plans, structural drawings, electrical schematics, plumbing layouts, and more. You’ll need to identify the materials required for each aspect of the build.
At this stage, it’s crucial to work with the most up-to-date drawings, as changes to the design can significantly impact the quantity of materials needed. Estimators must ensure that they are reviewing the latest revisions to avoid errors.
2. Identify Materials Required
Once the drawings have been reviewed, the next step is to identify and list all materials required for the project. This includes everything from basic structural materials like concrete and steel to specialized items like HVAC systems or electrical components. Each material should be clearly defined, including its type, grade, and any relevant specifications (e.g., dimensions or weight).
3. Measurement and Quantification
The key task in a Material Take-Off is the quantification of the required materials. This involves calculating the dimensions of various components and determining the amount of each material needed. For example, an estimator might measure the surface area of a wall to determine how much brickwork is required or calculate the length of wiring needed for an electrical system.
Quantities are typically expressed in standard units such as:
- Cubic meters (m³) for concrete or earthworks
- Square meters (m²) for flooring, roofing, or cladding
- Linear meters (m) for piping, wiring, or timber
4. Account for Waste
When performing a Material Take-Off, it’s important to factor in a percentage for material waste. This accounts for the unavoidable loss of materials that occurs during cutting, fitting, or transportation. Waste percentages vary by material, but it’s common practice to add a 5-10% buffer to ensure that you don’t run short of materials.
5. Compile the MTO Sheet
After all materials have been measured and quantified, the next step is to compile the data into a structured document known as the Material Take-Off Sheet. This sheet lists all the materials required, their quantities, units of measure, and any other relevant details (e.g., supplier, cost estimates).
At this point, it’s essential to cross-check the MTO sheet to ensure that nothing has been missed and that all quantities are accurate.
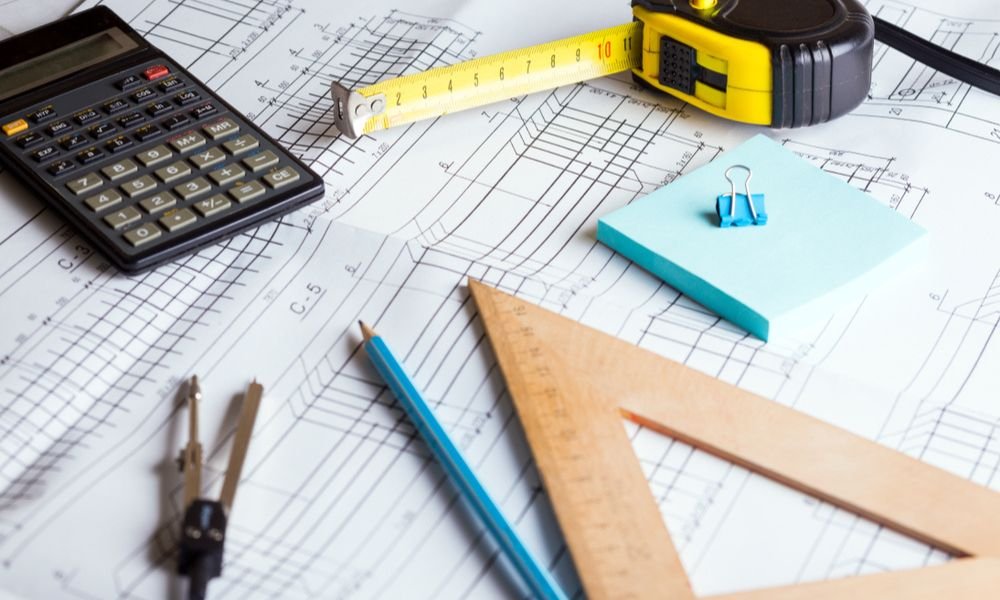
Types of Material Take-Off Methods
There are several different methods for performing a Material Take-Off, each suited to different types of projects. These include:
1. Manual Take-Off
In this traditional method, estimators use printed drawings, rulers, and calculators to manually measure dimensions and calculate material quantities. While this approach can be accurate, it’s also time-consuming and prone to human error, especially on large or complex projects.
2. Digital Take-Off
In a digital take-off, estimators use specialized software to measure and calculate quantities directly from digital drawings, such as PDFs or CAD files. Tools like Bluebeam Revu, PlanSwift, or Cubit allow users to measure dimensions with a click of the mouse, making the process faster and more accurate than manual take-offs.
3. 3D Model-Based Take-Off (BIM)
With the rise of Building Information Modeling (BIM), some take-offs are performed using 3D models of the project. These models include detailed information about the quantities and types of materials required for each element of the build. BIM-based take-offs are highly accurate and integrate well with other project management tools, but they require advanced software and expertise.
Common Mistakes to Avoid in Material Take-Offs
Even experienced estimators can make mistakes when performing a Material Take-Off. Here are a few common errors to watch out for:
1. Overlooking Small Items
It’s easy to focus on the major materials like concrete or steel and forget about the smaller components like screws, nails, or brackets. However, these small items can add up, both in terms of cost and quantity, so it’s essential to include them in the MTO.
2. Not Accounting for Design Changes
As projects evolve, design changes are inevitable. Failing to update the MTO to reflect these changes can lead to incorrect material orders, delays, and increased costs. Always ensure you’re working from the latest drawings and specifications.
3. Ignoring Supplier Lead Times
Some materials may have long lead times, especially if they are custom-made or imported. Failing to account for these lead times in your MTO can result in project delays. Make sure to consider availability when planning your material orders.
4. Incorrect Waste Factors
Underestimating or overestimating waste can lead to shortages or excess materials. Be realistic about the amount of waste that will occur based on the type of material and the nature of the work.
Tips for Improving Your Material Take-Off Process
1. Use Specialized Software
If you’re still relying on manual take-offs, consider investing in digital take-off software. Not only will this save time, but it will also improve accuracy by eliminating human error.
2. Double-Check Your Measurements
Accuracy is everything in a Material Take-Off, so always double-check your measurements and quantities. Small errors in measurement can lead to big problems on-site.
3. Work Closely with Your Suppliers
Good communication with suppliers can help ensure that you’re ordering the right materials in the right quantities. They can also advise on lead times, availability, and any potential issues with supply.
Master Your Material Take-Off for Successful Projects
An accurate and thorough Material Take-Off is a vital part of any successful construction project. By ensuring that you have the right materials, in the right quantities, at the right time, you can reduce waste, control costs, and keep your project running smoothly.
Whether you’re using manual methods or advanced digital tools, mastering the MTO process will improve your overall project efficiency and help you deliver on time and within budget.
Accurate material take-offs (MTOs) are the foundation of successful construction projects. Whether you’re looking to reduce costs, minimize waste, or ensure timely procurement, having a reliable MTO process is essential.
Let us help you streamline your material estimation process!
- Get a Free Consultation: Our experts are ready to assess your project needs and guide you toward efficient material planning.
- Customized Solutions: Tailored MTO services to fit your project’s specific requirements.
- Stay on Budget and On Schedule: Avoid delays and costly errors by using accurate and up-to-date material lists.
Contact us today to learn more about how our MTO services can elevate your next construction project!
👉 Request a Consultation or Contact Us