In the construction industry, both Quantity Take-Off (QTO) and Detailed Estimate play crucial roles in the project planning process. However, they serve distinct functions at different stages of a project. Understanding the difference between these two processes can improve project management, resource allocation, and budgeting.
In this blog, we’ll explore the differences between Quantity Take-Off and Detailed Estimate, how each is used, and which one is more appropriate for different phases of construction.
What is Quantity Take-Off?
Quantity Take-Off (QTO) is a preliminary process in which all the material quantities required for a construction project are measured and extracted from project drawings and documentation. It serves as the foundation for cost estimating, providing the basic data for determining material needs, labor, and equipment.
Typically, quantity take-off is carried out at the beginning of the planning phase, and its main objective is to provide an accurate account of the physical materials necessary to complete a project. For example, a QTO might include the number of bricks, meters of wiring, or cubic meters of concrete required to build a structure.
What is a Detailed Estimate?
A Detailed Estimate, on the other hand, is a more advanced process that includes not only material quantities but also the associated costs for labor, equipment, overhead, profit, and other indirect costs. Unlike QTO, which focuses primarily on materials, the Detailed Estimate provides a full breakdown of all project costs.
This estimate is typically prepared after the QTO and provides a more comprehensive understanding of the project’s financials. It is often used during the tendering and bidding process and is essential for project budgeting and financial planning.
Key Differences Between Quantity Take-Off and Detailed Estimate
Understanding the differences between these two processes is essential for successful project management. Let’s break down the key distinctions:
1. Purpose
- Quantity Take-Off: Focuses on calculating the amount of materials needed for a project. It provides raw data for the estimating team to build on.
- Detailed Estimate: Aims to provide a full picture of the project’s financial requirements. It includes not only material quantities but also labor, subcontractor fees, overheads, and profit margins.
2. Level of Detail
- Quantity Take-Off: Concentrates on quantifying raw materials. It’s less detailed in terms of cost and does not account for labor, equipment, or indirect costs.
- Detailed Estimate: Provides a complete breakdown of the project’s costs, including labor, equipment, subcontractor fees, and material costs.
3. Timing
- Quantity Take-Off: Typically performed during the early stages of project planning. It’s used to generate the base for cost estimation.
- Detailed Estimate: Usually carried out later, after the QTO is completed. It helps finalize the project budget and is often used during the bidding process.
4. User
- Quantity Take-Off: Primarily used by estimators and quantity surveyors to measure materials.
- Detailed Estimate: Used by contractors, project managers, and clients to assess overall project costs, submit bids, and secure funding.
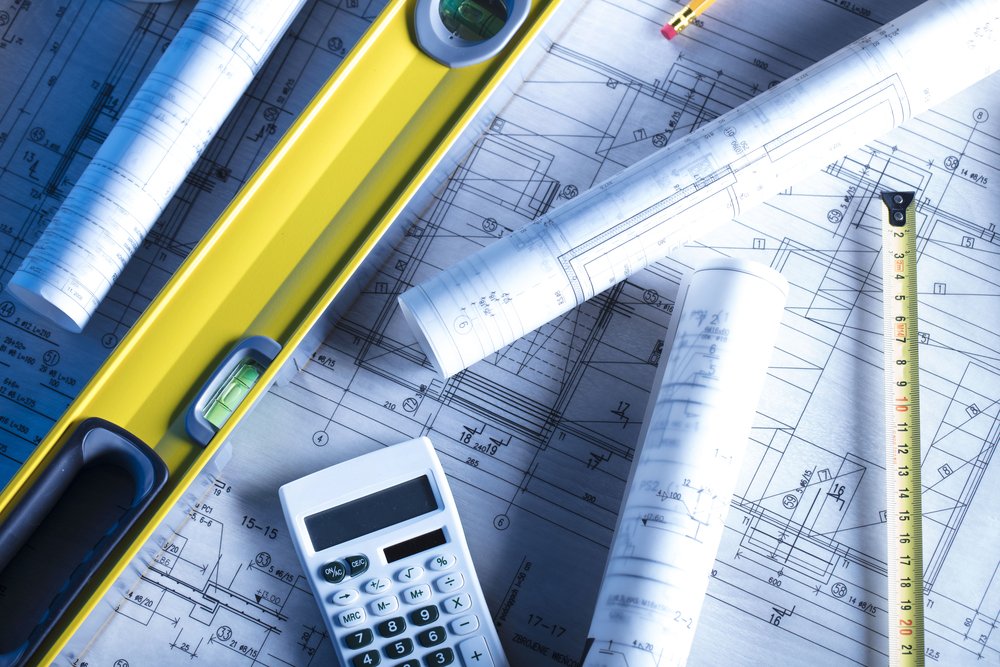
When Should You Use a Quantity Take-Off?
Quantity Take-Off is an essential tool at the start of a construction project. It helps estimators calculate the precise quantities of materials required, ensuring that the right amount of material is ordered and delivered to the site. Here are a few scenarios where using a QTO is especially helpful:
1. Initial Budgeting and Planning
The QTO provides the first glimpse into the material needs for the project. While it doesn’t include labor or equipment costs, it offers a solid foundation for creating an initial budget.
2. Procurement Planning
With an accurate QTO, the procurement team can coordinate material deliveries to ensure they arrive on-site when needed, avoiding costly delays.
3. Design Revisions
If the project undergoes any design changes, a new QTO can be generated to adjust material quantities accordingly.
When Should You Use a Detailed Estimate?
A Detailed Estimate is vital for finalizing the project’s budget and preparing for the bidding process. Contractors and clients rely on this estimate to determine the total cost of the project and ensure that it’s financially feasible. Here’s when you should use a Detailed Estimate:
1. Tendering and Bidding
The Detailed Estimate is typically prepared during the tendering phase. Contractors use it to provide accurate bids based on the full scope of the project.
2. Final Budgeting
This estimate provides a comprehensive view of all project costs, including labor, materials, and overhead. It’s used to set the project’s final budget and allocate resources.
3. Contract Negotiations
A Detailed Estimate can also help during contract negotiations, ensuring that all parties have a clear understanding of the project’s financials and that expectations are aligned.
How Quantity Take-Off and Detailed Estimates Work Together
Although QTO and Detailed Estimates are distinct processes, they are closely related and often work together to ensure accurate project planning and cost control. Here’s how:
- QTO feeds into the Detailed Estimate: The material quantities calculated during the QTO process are essential data points that the estimating team uses to develop a full project estimate.
- QTO for preliminary budgeting, Detailed Estimate for final costs: During the early stages of project planning, QTO provides initial material data, while the Detailed Estimate adds all necessary financial details later in the process.
- Revisions in QTO affect the Detailed Estimate: If there are changes in material quantities or design during the project, both the QTO and Detailed Estimate will need to be updated to reflect the new requirements.
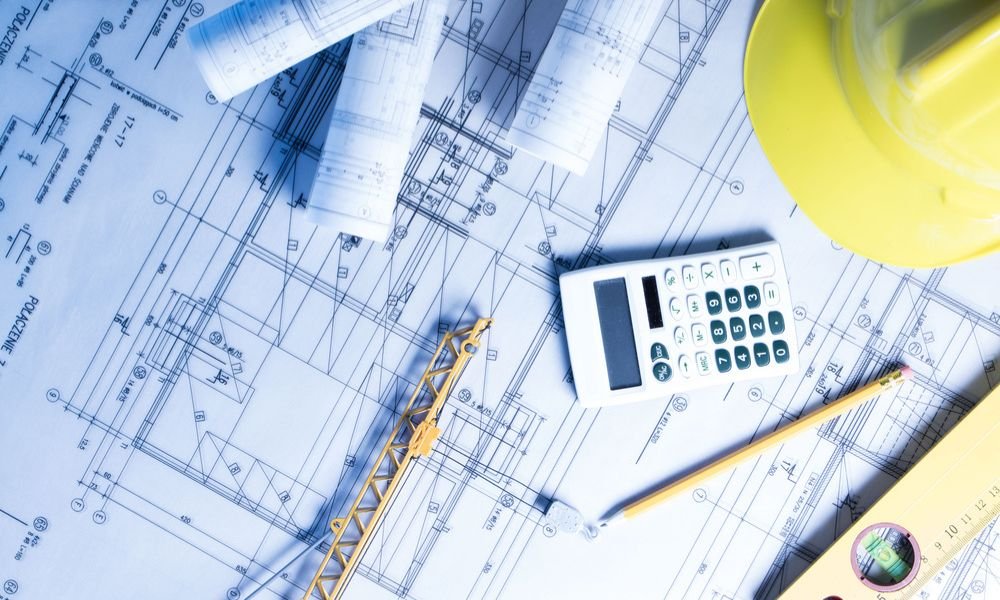
Best Practices for Accurate Quantity Take-Offs and Detailed Estimates
1. Use Digital Tools
Digital tools like Bluebeam Revu, PlanSwift, and Cubit can streamline both QTO and Detailed Estimates. These tools help reduce errors, speed up the measurement process, and provide better accuracy than manual methods.
2. Double-Check Measurements
Errors in the QTO process can lead to inaccurate estimates, so it’s essential to double-check all measurements and calculations. Cross-reference your material quantities with the project drawings to ensure everything is accounted for.
3. Collaborate with Subcontractors
When preparing a Detailed Estimate, involve subcontractors in the process. They can provide valuable insight into labor costs and specific materials required for their trades, which can improve the accuracy of your estimate.
4. Account for Contingencies
In any construction project, unforeseen circumstances can lead to additional costs. Always include a contingency in your Detailed Estimate to cover unexpected expenses, such as design changes or material price fluctuations.
Common Mistakes to Avoid
Even experienced estimators and project managers can make mistakes during QTO and Detailed Estimating. Here are some common pitfalls to watch out for:
1. Overlooking Small Items
When performing a QTO, it’s easy to focus on the big-ticket materials like concrete and steel and forget about smaller components like nails, screws, and adhesives. These small items can add up, so make sure they’re included in your calculations.
2. Failing to Update Estimates
Construction projects often experience changes, from design modifications to fluctuating material costs. Make sure your QTO and Detailed Estimates are regularly updated to reflect any project changes.
3. Ignoring Waste Allowances
Material waste is an unavoidable part of construction. Always account for waste when calculating material quantities in your QTO and adjust your estimates accordingly.
Understanding QTO and Detailed Estimates for Better Project Planning
Both Quantity Take-Offs and Detailed Estimates are essential tools for ensuring the success of construction projects. While the QTO focuses on the raw material quantities, the Detailed Estimate provides a complete breakdown of the project’s financials, including labor and overhead.
By understanding the differences between the two and knowing when to use each, you can improve project efficiency, reduce costs, and ensure that your project stays on track from start to finish.