In the world of construction, precision and accuracy are essential for any project’s success. Estimating the right amount of materials required for a construction project is crucial for controlling costs, avoiding delays, and ensuring that all phases of the build are executed smoothly. This process, known as Quantity TakeOff (QTO), forms the foundation of cost estimating and procurement planning in construction.
This guide will walk you through the complete process of performing an accurate Quantity Take-Off, including best practices, tools, and methods. Whether you’re managing a residential project or overseeing a large commercial development, mastering QTO will set your project up for success.
What is Quantity TakeOff?
A Quantity Take-Off (QTO) is the process of determining and measuring the quantities of materials required to complete a construction project. It involves extracting detailed quantities from project blueprints, architectural drawings, and design documents. The quantities obtained from the QTO process are then used to estimate the total material cost, schedule material deliveries, and plan the construction process.
The primary objective of a QTO is to calculate the precise amount of each material—such as concrete, steel, bricks, and timber—so that contractors can develop an accurate cost estimate and avoid both shortages and excesses during construction. It’s typically performed by quantity surveyors, estimators, or project managers, and is crucial for the overall success of a project.
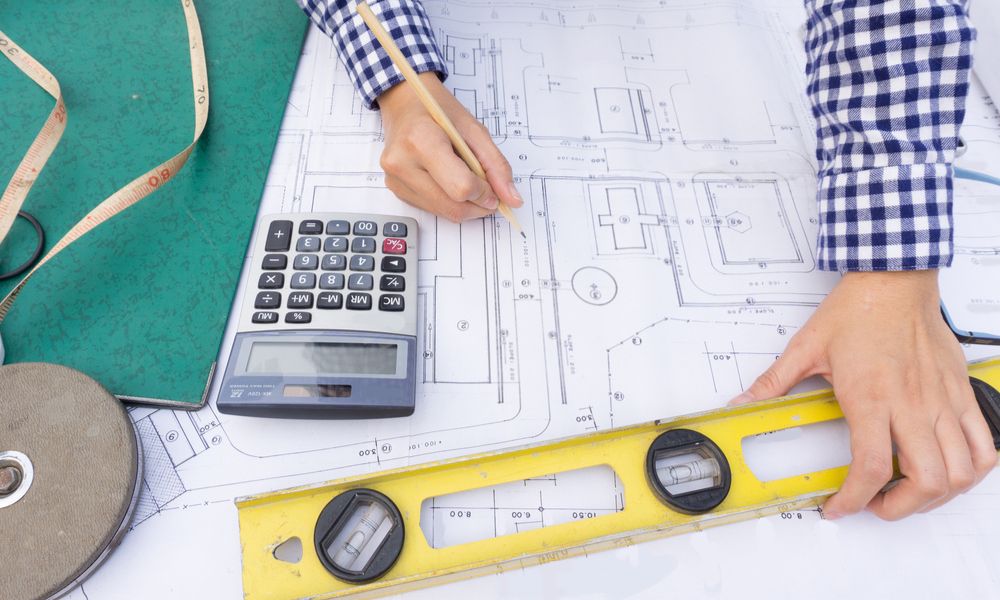
Why is Quantity Take-Off Important?
Performing an accurate Quantity Take-Off provides several essential benefits for construction projects:
Accurate Cost Estimation
QTO serves as the foundation for developing an accurate cost estimate. By calculating the exact quantities of materials required, contractors can build a realistic budget that covers the entire scope of the project. Without precise material quantities, there’s a higher risk of budget overruns or underfunding.
Efficient Procurement
Knowing the exact quantities of materials required allows procurement teams to plan their purchases efficiently. This means materials can be ordered in the right amounts and delivered at the right time, preventing delays and reducing storage needs.
Minimizing Waste
A well-executed QTO helps reduce material waste. Over-ordering can result in leftover materials that may never be used, while under-ordering can disrupt the project timeline due to delays in obtaining more supplies. QTO helps strike a balance by providing an accurate measure of what’s needed.
Project Planning and Scheduling
The data gathered from QTO also helps project managers develop a realistic project schedule. With an accurate understanding of material requirements, they can align labor and equipment resources to ensure the project progresses without unnecessary interruptions.
The Quantity Take-Off Process: Step-by-Step
Conducting an accurate QTO involves several key steps. Let’s break down the process.
Step 1: Review Project Drawings and Documents
The first step in performing a QTO is to thoroughly review all the construction drawings, blueprints, and specifications related to the project. This includes architectural plans, structural drawings, and engineering documents. Ensure that you are working from the latest versions of these documents, as changes in the design can impact the materials required.
During this step, it’s important to familiarize yourself with the scope of the project, identify key components, and gain a clear understanding of the materials that will be needed.
Step 2: Identify the Materials Required
Next, you need to identify all the materials required for each phase of the project. Start by breaking down the project into individual sections or components, such as the foundation, walls, roof, plumbing, electrical systems, and finishes.
For each section, list all the materials needed, including:
- Concrete and reinforcement
- Steel structures
- Timber and framing
- Brick and masonry
- Roofing materials
- Plumbing and electrical supplies
- Finishing materials (tiles, flooring, paint)
At this stage, you should specify the type, size, grade, and quality of the materials to ensure that the right products are ordered.
Step 3: Measure Quantities
Once you’ve identified all the materials required, the next step is to measure the quantities needed for each material. This involves calculating the dimensions and quantities of each component from the project drawings.
Common units of measurement include:
- Cubic meters (m³) for concrete and excavation.
- Square meters (m²) for walls, flooring, and roofing.
- Linear meters (m) for piping, wiring, and timber.
- Number of units for items like doors, windows, and fixtures.
To ensure accuracy, use appropriate measurement tools such as rulers, scales, and software to calculate the quantities. Modern software tools can automatically calculate quantities from digital drawings, making this step faster and more accurate.
Step 4: Account for Material Waste
Construction projects typically generate some degree of material waste due to factors such as cutting, installation errors, or transportation. It’s essential to account for waste when performing a QTO. The waste percentage varies by material type:
- Concrete and masonry: 5-10% waste factor.
- Roofing materials: 10-15% waste factor.
- Wood and timber: 5-10% waste factor.
Adding a waste allowance to your QTO ensures that you don’t run short of materials and can prevent costly delays caused by reordering supplies.
Step 5: Compile the Quantity Take-Off Sheet
After measuring the quantities and accounting for waste, it’s time to compile everything into a structured Quantity Take-Off Sheet. This sheet should include:
- Material description
- Units of measure (e.g., cubic meters, square meters, linear meters)
- Quantities required
- Waste allowance
- Total quantities
The QTO sheet serves as a reference for material ordering, budget development, and project planning. It should be well-organized and easy to update as the project evolves.
Step 6: Verify the Data
Before finalizing the QTO, it’s crucial to verify the accuracy of your measurements and calculations. Double-check the quantities against the project drawings to ensure nothing is missing or incorrectly measured. A second estimator or supervisor can also review the QTO for added assurance.
Digital Tools for Quantity Take-Off
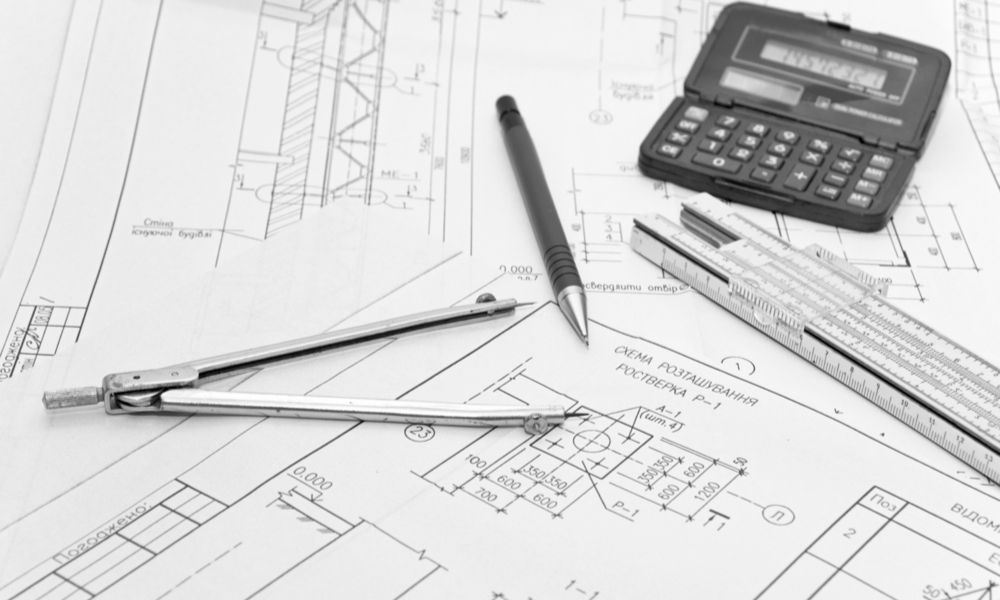
While traditional QTOs are done manually, modern technology has made the process much more efficient and accurate. Here are a few digital tools that can help streamline QTO:
Bluebeam Revu
Bluebeam Revu is a popular digital tool for performing QTOs. It allows users to measure quantities directly from digital PDF drawings and offers powerful markup tools for collaboration. By using Bluebeam, estimators can quickly extract material quantities, reducing the time spent on manual measurements.
PlanSwift
PlanSwift is another widely-used software for QTO that allows users to measure quantities from 2D digital drawings. With its easy-to-use interface, PlanSwift can calculate areas, lengths, and volumes in a fraction of the time it takes to do it manually. It also integrates with cost estimating features, making it a versatile tool for project planning.
Cubit
Cubit offers 3D take-off capabilities, allowing for more advanced and precise measurements. It supports both 2D and 3D project models, making it ideal for more complex projects. Cubit is also capable of integrating with other project management tools, ensuring that material quantities align with budgets and schedules.
Common Challenges in Quantity Take-Off
Even with the best tools and practices, QTO can present some challenges. Here are a few common challenges to be aware of:
Inconsistent Units of Measurement
Ensure that all measurements are recorded consistently using standard units. Mixing units (e.g., switching between cubic meters and square feet) can lead to errors in the final quantities.
Omitting Smaller Items
It’s easy to overlook small but essential materials like fasteners, adhesives, and insulation. These items may seem minor, but they add up, and omitting them can cause delays in construction.
Failing to Update for Design Changes
Construction projects often experience design changes or revisions. If the QTO isn’t updated to reflect these changes, it can lead to material shortages or over-ordering.
Mastering Quantity Take-Off for Successful Construction Projects
Quantity Take-Off is a critical process for ensuring that construction projects run smoothly, stay within budget, and avoid costly delays. By following the steps outlined in this guide—reviewing project documents, measuring quantities accurately, accounting for waste, and leveraging digital tools—you can perform accurate QTOs that set your project up for success.
Mastering Quantity Take-Off will not only improve the efficiency of your construction projects but also enhance your ability to manage costs and schedules effectively.