In the construction industry, accurate estimates are critical for project success. A Quantity Take-Off (QTO) is one of the most essential processes in developing these estimates. It involves determining the quantities of materials needed for a construction project based on the project’s architectural and engineering drawings.
In this blog, we’ll dive deep into what a Quantity Take-Off is, why it’s important, the steps involved, and how digital tools can simplify the process.
What is a Quantity Take-Off?
A Quantity Take-Off (QTO) is the process of calculating the quantities of materials required for a construction project. This is usually done by examining project drawings and documents to measure various building elements, such as walls, floors, ceilings, foundations, and more.
The results of a QTO form the basis for the project’s cost estimate and procurement plan. Whether you’re building a house or a large-scale commercial complex, having an accurate QTO ensures that the right amount of materials are ordered, preventing delays and overruns.
Why is a Quantity Take-Off Important?
The success of a construction project hinges on accurate planning. Here are some reasons why QTO is essential:
Accurate Budgeting and Cost Control
A proper QTO helps determine how much each material will cost, allowing for an accurate overall project budget. By knowing the exact quantities of materials, estimators can calculate costs more precisely, reducing the chances of overspending.
Efficient Procurement
An accurate QTO ensures that you order the correct amount of materials for the project. This avoids the risks of material shortages or over-ordering, both of which can cause delays or add unnecessary costs.
Project Scheduling
Knowing the materials needed at each phase of the construction process enables better project scheduling. Materials can be ordered to arrive just in time, keeping the project on track and preventing site congestion from excess materials.
Minimizing Waste
Accurate material estimation reduces waste. Ordering just the right amount of materials helps construction teams avoid leftover materials that are difficult to reuse, contributing to cost savings and sustainability efforts.
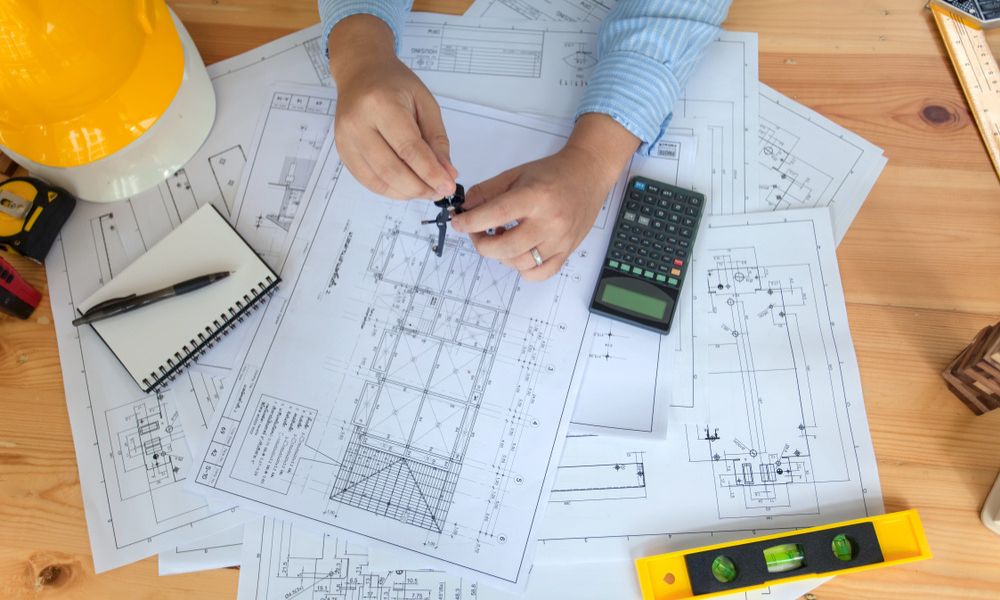
The Quantity Take-Off Process: Step-by-Step
Let’s break down the key steps involved in performing a Quantity Take-Off:
Review Project Drawings
The first step in performing a QTO is thoroughly reviewing the project’s architectural and engineering drawings. These documents provide the dimensions and specifications required to calculate material quantities.
Identify Materials
Once the drawings have been reviewed, the next step is identifying all the materials required for the project. This includes things like concrete for the foundation, timber for framing, steel for reinforcement, and finishing materials like drywall and flooring.
Measure Quantities
Next, measure the quantities of each material using the project drawings. This involves calculating areas, lengths, volumes, and numbers of units for items such as doors and windows. Estimators may use different units of measurement:
- Cubic meters (m³) for concrete or soil
- Square meters (m²) for wall coverings, flooring, or roofing
- Linear meters (m) for pipes, wires, or framing members
Account for Material Waste
In any construction project, a certain amount of material waste is inevitable due to cutting, errors, or design changes. Always include a percentage of waste for each material to ensure that the project doesn’t run short. Typical waste allowances vary depending on the material:
- 5-10% for concrete
- 10-15% for roofing materials
- 5-10% for timber
Organize Data into a Take-Off Sheet
Once all measurements are complete, organize the data into a structured take-off sheet that includes:
- Material descriptions
- Units of measurement
- Quantity required
- Waste allowance
- Total quantity to be ordered
This take-off sheet will serve as the primary reference for material procurement and cost estimation.
Manual vs. Digital Quantity Take-Offs
Historically, QTOs were performed manually, with estimators measuring printed drawings using rulers and scales. However, this method can be time-consuming and prone to human error. Today, digital take-off software has revolutionized the process, offering faster and more accurate measurements.
Manual Take-Offs
Manual take-offs are still used for smaller projects or when digital drawings aren’t available. However, they require careful attention to detail and are more prone to mistakes due to the manual nature of the work.
Digital Take-Offs
Digital take-off software, such as Bluebeam Revu, PlanSwift, or Cubit, enables estimators to measure quantities directly from digital drawings. This method is more efficient and accurate than manual take-offs, reducing the likelihood of errors and allowing for faster project turnaround.
Key benefits of digital take-offs include:
- Accuracy: Digital tools help avoid mistakes in measurements, ensuring more precise material quantities.
- Speed: Automated calculations reduce the time needed to complete a QTO.
- Integration: Many digital tools integrate with cost-estimating software, making it easier to generate full project estimates.
- Collaboration: Multiple team members can access and work on the same project drawings in real-time.
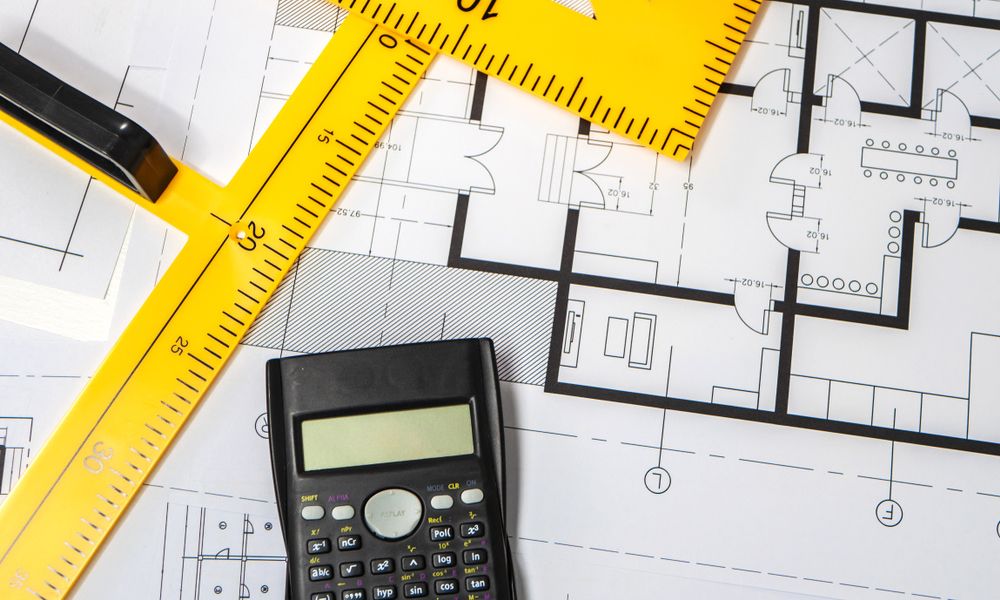
Best Practices for Accurate Quantity Take-Offs
To ensure the accuracy and efficiency of your QTO process, follow these best practices:
Double-Check Your Measurements
Even with digital tools, it’s essential to double-check measurements to avoid errors that could throw off the entire estimate.
Stay Updated on Project Changes
Design changes are common in construction projects. Make sure your QTO reflects the most up-to-date drawings and specifications to avoid discrepancies.
Collaborate with Subcontractors
Subcontractors can provide valuable insights into material requirements, especially for specialized tasks such as electrical work or plumbing. Collaborating with them during the take-off process ensures that nothing is overlooked.
Use Digital Tools When Possible
Leverage digital take-off software to speed up the process, improve accuracy, and reduce human error. These tools also make it easier to update quantities when project changes occur.
Mastering Quantity Take-Offs for Successful Projects
A well-executed Quantity Take-Off is critical to the success of any construction project. By following the steps outlined in this guide—reviewing drawings, identifying materials, measuring quantities, and accounting for waste—you can ensure that your project runs smoothly, stays on budget, and avoids costly delays.
Whether you’re using traditional manual methods or digital tools, the key to a successful take-off is accuracy. Mastering the QTO process will give you the confidence to manage any construction project efficiently.
Whether you’re a contractor, estimator, or project manager, mastering quantity take-offs is essential for accurate project planning and budgeting. Don’t let manual errors or inefficiencies slow down your workflow. Leverage the right tools and expertise to ensure precise estimates and smooth project execution.
Contact us today to learn more about our take-off solutions or request a demo. Let us help you deliver accurate results, improve your efficiency, and save time on every project.