Performing a Material Take-Off (MTO) is a crucial step in any construction project. Without an accurate MTO, you risk running short on materials or over-ordering, both of which can increase costs and delay project timelines. Whether you’re managing a small residential build or a large commercial project, understanding how to perform a proper MTO will save you time, money, and headaches.
This guide will provide a comprehensive step-by-step process to ensure you’re executing material take-offs effectively and efficiently.
What is a Material Take-Off?
A Material Take-Off is the process of listing and quantifying all the materials needed to complete a construction project. It’s a critical part of estimating that breaks down the raw materials required from architectural drawings and engineering plans. The MTO serves as the foundation for project costing, procurement, and planning.
This document is typically created by a quantity surveyor, estimator, or project manager, and it includes everything from structural elements like concrete and steel to smaller items like screws and nails. A well-executed MTO ensures that the project runs smoothly by providing accurate information for budgeting and material procurement.
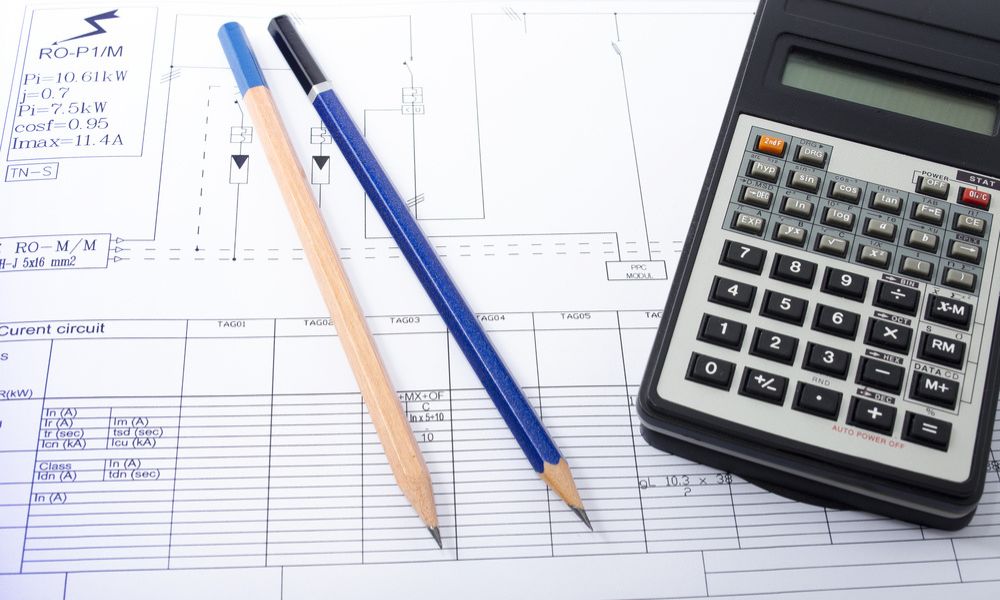
Why is a Material Take-Off Important?
Accurate material take-offs are essential for several reasons:
Budgeting
A Material Take-Off is the backbone of a project’s budget. Knowing how much of each material is needed allows for accurate cost estimation, which prevents budget overruns or unexpected expenses down the line.
Procurement Planning
With a detailed MTO, procurement teams can schedule deliveries based on when materials will be needed during the construction process. This prevents the site from being overcrowded with unnecessary materials and ensures that critical supplies are on hand when required.
Waste Reduction
By calculating the exact quantities of materials, an MTO helps minimize waste. Over-ordering results in excess materials that may go unused, while under-ordering can lead to costly delays if supplies run out mid-project.
Project Scheduling
An accurate MTO helps in sequencing tasks efficiently. It allows project managers to plan the timing of material delivery and labor coordination, keeping the project on schedule.
How to Perform a Material Take-Off: A Step-by-Step Process
Here’s a step-by-step guide to help you carry out a comprehensive and accurate Material Take-Off.
Step 1: Review the Construction Drawings
Before you begin, gather all relevant construction documents, including architectural plans, structural drawings, and detailed engineering specifications. These drawings provide the layout, dimensions, and design elements required to measure material quantities.
Make sure to verify that you are working with the latest version of the plans, as changes during the design phase are common. Failing to account for updated drawings can lead to major errors in your MTO.
Step 2: Identify the Materials
Once you’ve reviewed the drawings, identify all the materials required for the project. Break the project down by phases or sections (e.g., foundation, walls, roofing, plumbing, etc.) and list the materials needed for each phase.
Here are some common materials you’ll typically need to account for:
- Concrete
- Steel reinforcement
- Timber
- Bricks or masonry
- Roofing materials
- Plumbing fixtures
- Electrical wiring
For each material, note the specifications, such as size, grade, or thickness. This level of detail ensures that you’re ordering exactly what the project requires.
Step 3: Measure Quantities
The next step is to measure the quantity of each material directly from the construction drawings. Depending on the material, you’ll use different units of measurement:
- Volume (cubic meters): Used for concrete, earthworks, or backfill.
- Area (square meters): Applied to surfaces like walls, flooring, and roofing.
- Length (linear meters): Used for piping, wiring, and structural steel.
- Count (units): For items like windows, doors, or fixtures.
Accurate measurement is key. For example, when measuring walls, calculate the surface area to determine the amount of brick or plaster required. When working with rebar, calculate the length and gauge needed to support the structural load.
Step 4: Account for Waste
Every construction project has a certain level of material waste due to cutting, handling, or installation. To avoid running short on materials, add a waste allowance to each item. The standard waste percentage varies by material:
- Concrete and bricks: 5-10%
- Roofing materials: 10-15%
- Tiles: 5-10%
Factor in waste for every material in your MTO to ensure you have enough on hand, especially for items that are cut to fit.
Step 5: Document the Quantities in a Take-Off Sheet
Once you’ve measured and accounted for waste, compile all the data into a Material Take-Off Sheet. This document should clearly list:
- Material type
- Material specification (size, grade, thickness, etc.)
- Quantity required (with units of measurement)
- Waste allowance
- Total quantity
The MTO sheet provides a structured summary of the materials required and can be shared with suppliers, contractors, and procurement teams for accurate ordering.
Step 6: Verify and Cross-Check
Before finalizing the MTO, double-check your measurements and calculations. One small error can lead to significant cost overruns or delays. Cross-reference your material quantities with the project drawings and check for consistency.
It’s also advisable to have a second estimator or quantity surveyor review the take-off to catch any discrepancies or potential mistakes.
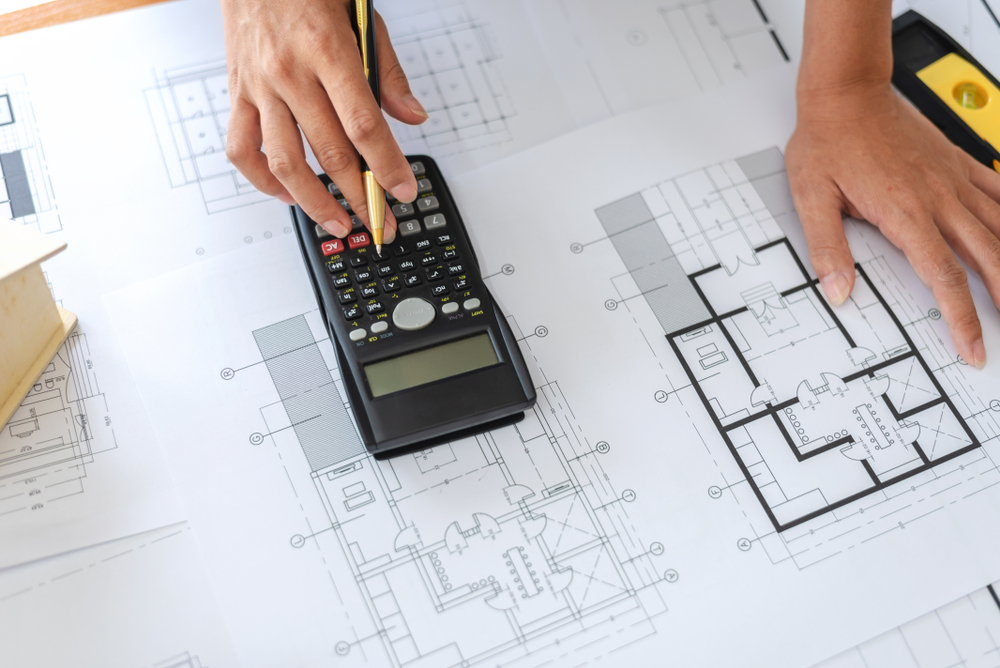
Digital Tools for Material Take-Offs
Traditionally, Material Take-Offs were performed manually, using rulers, scales, and calculators. Today, there are digital tools available that speed up the process and improve accuracy. Here are some popular digital take-off tools:
Bluebeam Revu
Bluebeam Revu is one of the most widely used digital take-off tools. It allows users to measure directly from digital PDF drawings and mark up construction documents for easy collaboration. The software automates the measurement process, reducing the risk of errors associated with manual calculations.
PlanSwift
PlanSwift is another popular software for digital take-offs. It enables estimators to calculate quantities directly from 2D digital drawings, offering drag-and-drop functionality for measuring areas, lengths, and volumes.
Cubit
Cubit is a 3D model-based software that allows you to measure from both 2D plans and 3D models. It’s especially useful for complex projects where visualizing the materials in 3D helps improve accuracy.
Common Mistakes to Avoid in Material Take-Offs
Even with experience, mistakes can happen during Material Take-Offs. Here are some common pitfalls to avoid:
Missing Items
It’s easy to overlook smaller components like screws, brackets, or adhesives when focusing on large materials like concrete or timber. Ensure that every material required for the project, big or small, is included in your MTO.
Not Accounting for Design Changes
Designs evolve as projects progress. If you fail to update the MTO to reflect these changes, you might end up ordering the wrong materials or insufficient quantities.
Underestimating Waste
Underestimating waste can result in material shortages, which cause project delays. Always include a realistic waste percentage for every material in your take-off.
Inconsistent Units of Measurement
Ensure that all measurements are recorded consistently using standard units. Converting units incorrectly can lead to errors in quantity calculations.
Master Your Material Take-Off for a Smooth Construction Process
An accurate Material Take-Off is essential for the successful execution of any construction project. It ensures that you have the right materials, in the right quantities, at the right time. By following the steps outlined in this guide—reviewing drawings, measuring quantities, accounting for waste, and using modern digital tools—you can ensure that your project stays on track and within budget.
Remember, a well-prepared MTO leads to fewer delays, lower costs, and a more efficient construction process. With the right approach, mastering Material Take-Off will become a key asset in your project management toolkit.